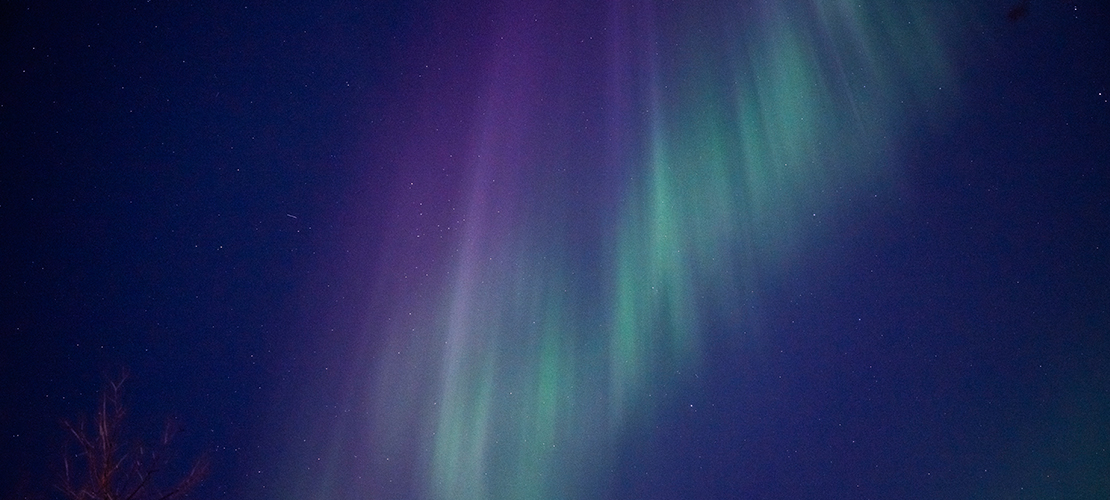
Since 2022, Ingersoll — a community of 13,700 people in southwestern Ontario — has been home to one of Canada’s first full-scale electric-vehicle (EV) manufacturing facilities: General Motors’ CAMI Assembly plant.
CAMI’s transition from producing Chevrolet Equinox gas-powered SUVs to fully electric delivery vans revived the plant and the community’s prospects. But the journey has been bumpy. The plant’s temporary shutdown while it retooled came on the heels of a strike in 2019, the COVID-19 pandemic the following year and then a global shortage in semiconductors and other parts. The disruptions led to temporary and permanent layoffs in the community. Meanwhile, the new plant requires fewer workers with different skills.
Ingersoll’s experience offers some lessons on the challenges of managing a workforce transition, highlights the vulnerability of a community dependent on a single major employer and illustrates how the global shift to lower carbon emissions can affect auto production, workers and communities at the local level.
Still, there is much to be optimistic about. Ingersoll is part of a broader ecosystem of EV investments in southern Ontario, including several battery plants and a $15-billion investment by Honda aimed at securing the long-term sustainability of automotive and parts manufacturing in southern Ontario.
Ingersoll is situated on some of Canada’s best agricultural land, and its proximity to major transportation networks, the Greater Toronto Area and the U.S. provide additional advantages.
While Ingersoll’s transformation is a community success story, questions remain about how it is being managed and whether workers, employers and the community have the support they need. The possibility of U.S. tariffs and changes to EV policy adds to the uncertainty.
Automotive industry changes
GM’s CAMI Assembly plant is a case study in how a manufacturing operation pivoted from the threat of closure and massive layoffs to becoming a leader in the transformation of the auto manufacturing sector.
The plant is one of the biggest employers in Ingersoll. In 2021, GM announced it would move production of the Chevy Equinox SUV from Ingersoll to Mexico earlier than expected. Rumblings that this was in the works began well before that date and led to a strike in 2017, following the loss to Mexico of another GM vehicle that had also been produced at the Ingersoll plant.
Production of the Equinox stopped in April 2022 and the plant remained closed until October while it retooled to produce electric BrightDrop delivery vans. The transition was good news for the community. However, the new auto-assembly operation employs fewer workers, and there have been repeated temporary layoffs during its transition.
“The workforce at GM has gone from 2,600 three years ago to 1,450 today,” said Mike Van Boekel, plant chairperson for Unifor Local 88, the union that represents many of the workers. “The plant has only been operating for 60 weeks in the last four years,” he added.
What’s more, fewer people are needed to make the new electric commercial vehicles than the SUVs produced previously. Delivery vehicles have fewer traveller comforts, and much of the work is automated. Fortunately, most of the workforce reduction took place at a time of major retirement and attrition, said Van Boekel.
GM workers spoke with hope and pride about doing something positive to address climate change, about being on the leading edge of the new green economy, about the plant’s reputation as an award-winning production facility, and about the prospect of establishing Ingersoll and Canada as a hub for electric-vehicle manufacturing and battery technology. But they also raised concerns about the precariousness of the new venture.
Several interviewees expressed concern that the uptake and infrastructure for EVs might not happen and that this sector, this community and these jobs will again be vulnerable. Finding jobs is less of a concern for workers than finding well-paid, unionized jobs, the interviewees said. It’s a challenge for workers seeking to meet personal financial obligations and sustain their standard of living.
“There are lots of jobs in this area but most of them are poor-paying service jobs, $18 to $20 an hour,” said Van Boekel. “Both GM and Toyota pay $30 to start for production. Tradespeople at GM start at the top rate of $52 per hour,” he added, “but these rates have to be competitive to attract the cream of the crop.”
The effect of losing some CAMI jobs has had a domino effect on the community. The United Way saw an increase in demand for the services it funds and Unifor opened a food bank at the union hall. Several auto parts suppliers shut down and local grocery stores, coffee shops and merchants were also affected, interviewees said.
Butcher Engineering, a parts manufacturer based in Ingersoll that used to build front-end modules for the CAMI plant, and Cooper-Standard, located in Glencoe, less than an hour’s drive away, closed their doors after production of the Equinox was moved to Mexico. More than 100 workers were employed at the Cooper-Standard plant, which produced gas lines, when they received the notice of closure in June 2023.
Some parts suppliers may be more affected by the transition to EVs than others. Those that supply items such as gas lines could see more changes in demand for their products than those supplying parts for the shells of vehicles.
In a seven-minute documentary created by Unifor, union members shared their thoughts and feelings about the transition of the plant. Some described how the ups and downs have affected families on a personal level; others talked about how it affected the broader community, including local restaurants and coffee shops.
The transition has been a challenge for GM too. “No one could have forecast the ups and downs,” said Bill Harkness, CAMI plant director. Building a market for a new product isn’t easy, he said. “There will be ebbs and flows.”
Land-use battles: Balancing agriculture with development
In addition to manufacturing, Ingersoll has a long history of agriculture and cheese production. Today, the region has a mix of crop, dairy and animal production.
The growth in manufacturing has led to some challenges as Ingersoll tries to balance agricultural land use with the need for land associated with new development, said Curtis Tighe, the Town of Ingersoll’s director of economic development and tourism.
Tighe noted that it took 14 years of negotiation to gain 1,500 more acres of farmland for the town’s residential and industrial development, but the listening, discussions and negotiations were part of a balanced strategy to help Ingersoll grow sustainably over the next 25 years.
This has met with some resistance from local farmers. Agricultural land “should be seen as a natural resource like water or trees … essential for life,” said Gordon Stock, a farm business owner. For him, protecting the area’s prime, productive agricultural land is about maintaining a sustainable food supply.
“The more food that has to come from out of the province, the more fossil fuel is burned,” he said. “We just end up outsourcing our carbon emissions overseas.”
In Wilmot Township, about a 45-minute drive north of Ingersoll, local farmers are fighting efforts by Waterloo Region to expropriate agricultural land to make way for a potential industrial megasite. The effort is part of a move by the Ontario government to assemble large tracts of land to attract global companies seeking to build EV and battery plants, and other projects.
In a region primed for growth and development, land use is an urgent challenge for farmers and municipalities alike. This is especially true as wind-energy developers enter the scene. In addition, agriculture is competing with manufacturing for access to a sustainable, reliable, affordable supply of electricity.
Farmers also fear the potential for increased costs associated with efforts to reduce greenhouse-gas emissions. As Stock sees it, the federal government should recognize how adaptive the agricultural industry has already been. “Rather than punitive policies for green transitions in agriculture, we need to work together, have a constructive, balanced approach,” he said. “They can’t set targets and mandates before the technologies and solutions have been proven. There’s a sense that no one cares how you do it, just get it done — so that’s when farmers get exasperated and frustrated.”
Some interviewees mentioned an outspoken pocket of resistance in the region that presents an obstacle to moving forward on the green energy transformation.
Adam Funnell, past president of the Ingersoll Chamber of Commerce, small business owner and financial planner, said the anti-change group is expressing a minority opinion. “Too much media attention is given to the vocal minority and to these hot-button stories. This is what politicizes and charges people up,” he said.
“We need to tone down the rhetoric and get people working together,” added Tighe.
But interviewees also recognized that many thoughtful people with complaints and criticism have valuable questions and insights that must be part of the dialogue. “Just because you ask a hard question doesn’t mean you’re someone who denies climate change or is against progress,” said Stock, the farm owner.
“Changing behaviour is a slow process and will take time,” added Allan Simm, general manager of Community Futures Oxford, a small federally funded business-support centre. “Many entrepreneurs are being put in the role of educating the public about sustainability products and practices, about the circular economy.”
Socio-economic issues
Like many communities across Canada, Ingersoll is grappling with shortages in housing, health care and other services, which have been exacerbated by a recent influx of newcomers to the area, new immigrants to Canada as well as retirees and families with young children who are relocating from elsewhere in the province.
“The biggest challenge here is housing: there’s not enough, it’s not affordable and there’s no room to build them,” said Funnell of the Ingersoll Chamber of Commerce.
Mark Gee, a union official for Unifor Local 88, said, “CAMI still has some of the highest- paying jobs but even those workers can’t get into the housing market without two incomes. And when both partners work at a single employer, there is still the constant fear of layoffs.”
The lack of affordable housing is also a problem for attracting new workers to the area. Employers are already struggling with labour shortages and local governments, who rely on the much-needed working-age population for a stable tax base, are also affected.
“The number one issue for local businesses is finding and keeping employees,” said Funnell. He pointed to another major local employer facing similar problems: “Trucking is growing and constantly hiring. We’ve got an urgent need to get products to market.” Some factories are busing people in from other areas, such as Hamilton, to work in Ingersoll’s manufacturing plants, he added.
Kelly Gilson, executive director of the United Way Oxford, which serves the town of Ingersoll, said the community has gone through four tumultuous years. “It was very tough,” she said. “GM CAMI Assembly and Unifor Local 88 employees are a family to us. They have always given financially to the United Way, and they also volunteer their time to support us and their community. From the beginning they’ve been there when we needed them, so it was important that we were there for them during their difficult time.”
She recalled receiving a thank you note from one laid-off GM worker who said she had been a longtime donor to the organization and never thought she would one day be using its services. The plant closure has affected not only GM employees, Gilson added. It has had a ripple effect across the community and has increased demand for the services the United Way funds.
The toll extends beyond financial considerations. “There was a social toll on individuals and the community itself,” she said. But now there is a sense that “we seem to be on the other side,” added Gilson. “There is definitely a sense of hope and excitement for the future,” she said.
“These are fundamental changes in how our community operates: poverty, homelessness, mental health, food security, transportation and especially lack of affordable and available housing,” said Jeff Surridge, CEO of Community Employment Services, a non-profit corporation serving Oxford County that provides help with training and job-hunting.
This sentiment was echoed by Allan Simm of Community Futures Oxford. “Affordable housing is a big challenge. The rise in homelessness and mental wellness particularly affects main-street businesses. Sustainability is one thing, but this is a top priority.”
The arrival of electric vehicle and battery production facilities in Ingersoll has created a buzz about the potential for the community to become a hub for clean-tech manufacturing.
Governments have played a major role in securing the investments. In April 2022, the Canadian government announced a $259-million investment that included money to transform the CAMI plant into “the first full-scale commercial electric vehicle production facility in Canada.” The Ontario government made a matching contribution.
Additional EV investments in southern Ontario include a federal-provincial partnership with Volkswagen for EV battery production in St. Thomas and with Toyota to support hybrid vehicle production in Cambridge and Woodstock. Other Ontario facilities for EV battery production and battery separation have been announced in Windsor by Stellantis, partnered with LG Energy Solution. In addition, Honda has pledged to invest $15 billion to build four new EV and battery manufacturing plants in Ontario. The federal and provincial governments have committed billions more to support the projects in Ontario and elsewhere.
Ingersoll’s proximity to U.S. markets, to Ontario’s Highway 401 and to the Greater Toronto Area makes it a favourable location for automotive assembly and parts production, according to Tighe, the town’s economic development officer. “Within one hour, there are several big cities as well as a workforce of 2.2 million working-age people,” he said.
Motor vehicles and parts account for a significant portion of trade between Canada and the U.S. Canadian exports of motor vehicles and parts to the U.S. totalled $84.9 billion in 2023 and imports totalled $83.2 billion. The Canadian auto industry is largely concentrated in southern Ontario because of the area’s proximity to the U.S. Ingersoll is located about 200 kilometres from Windsor, a major border crossing. With close cross-border integration, the sector is particularly susceptible to U.S. tariffs or changes in policy that affect the type of vehicles consumers buy.
The region is also considered a promising setting for renewable energy production, with good solar and wind assets, and it is situated on prime agricultural land.
According to one study, Ingersoll is located in an area with high soil quality and productivity. “Only 5 per cent of the Canadian land mass is made up of prime land. Only 0.5 per cent of it is Class 1, which is the best for growing crops. The Central Ontario Zone [in which Ingersoll is situated] is fortunate to contain a significant portion of this very limited resource. Unfortunately, it occurs in one of the fastest-growing regions of the country,” the report states.
Ontario farms are increasingly integrating renewable energy. According to Statistics Canada’s 2021 Census of Agriculture, the number of farms in the province reporting renewable energy production increased by 63.8 per cent to 8,483 in 2021. These farms accounted for 17.5 per cent of total farms in Ontario, the highest proportion in any province, and above the national rate (11.9 per cent).
“Farmers and agri-food businesses have been proactive in adapting to and managing massive transformations in products, practices and techniques, equipment and suppliers, farm size, transportation to markets, packaging, storage and energy usage,” said Gordon Stock, the farm business owner. “Farmers in the region have already been innovating on more planet-friendly farming practices and adapting to climate-related issues.”
A sense of resourcefulness and a “getting on with it” spirit was a theme in many of our interviews. There is a long-standing pride in the area’s manufacturing, agriculture and food-production base — from the early 1900s, when there were almost 100 cheese factories, to today’s heavy manufacturing.
“Ebbs and flows in consumer demand have always affected manufacturing, but we have a long-standing entrepreneurial spirit,” said Tighe. “We’ve risen to the challenge and grown steadily over time.”
Most interviewees spoke enthusiastically about the Ingersoll area’s economic potential. There is a “positive feel,” according to Tighe. “Town council has been quite progressive and intentional to position Ingersoll as a growth-oriented community,” and has been busy “branding all the community has to offer,” he said.
Ingersoll has experienced record economic growth in the last few years, Tighe added. “It’s a competitive world and we are competing against the world, and against our neighbours for investments. So, we have to be smart and think long-term. We are already punching above our weight for a town of this size.”
EV and battery manufacturing provide significant opportunities for Ingersoll to have secure, well-paying jobs. The federal government has pledged to phase out the sale of gas-powered vehicles by 2035. But several interviewees said government leadership and timely decision-making are needed to ensure robust electric vehicle uptake. Possible changes to U.S. policy could also affect EV demand in a critical export market for Canada.
Consumers “need to have trust” that the transition to EVs is going to happen, said Bill Harkness, CAMI plant director. And they need to see evidence of investment in infrastructure. Governments have invested heavily in manufacturing but have pulled back from offering rebates on EV purchases, he noted.
The federal government offers consumers and businesses purchase incentives on new EVs, but the program is set to expire within the next two years. Some provinces also offer rebates on EV purchases, but Ontario doesn’t.
“Investing in manufacturing is essential but artificial if you don’t invest in building the market,” Harkness said.
Expanding EV and electricity infrastructure, including power lines, charging stations, battery disposal facilities and electricity production, will also be critical. EV plants are large users of electricity, much larger than traditional auto assembly plants, and having a reliable source of electricity is essential for production.
In an emailed response to questions, GM noted that charging infrastructure in Canada is lagging, and pointed to a study prepared for Natural Resources Canada that forecasts that Canada will need to install roughly 40,000 public charging ports a year between 2025 and 2040. A lack of maintenance is also a challenge, with too many existing chargers out of order.
Critical minerals are another important consideration. Canada has rich deposits of critical minerals needed for battery production, but “the minerals in the ground have little value until they are processed,” the company said. China currently dominates global critical mineral processing.
In addition to financial investments, a successful energy transformation will require timely decision-making. “We are concerned that provincial and federal governments are not making decisions quickly or strategically for building the infrastructure that greener energy will need to thrive,” said Funnell, of the Chamber of Commerce. “Decision-makers in government really need to get behind the transition in meaningful, practical ways.”
“I’m still worried that politics and personalities will get in the way of solutions and moving forward,” he added. “Is there actually any political will for this?” he asked.
“Green sustainability initiatives are creeping into every sector and people are jumping on a lot of things but it’s hard to proceed when there is uncertainty about which way the economy is going, which way sustainability policies and supports are going,” added Surridge. “There are too many political unknowns.”
It’s a concern shared by workers. “Will the right decisions happen?” asked Charlotte Johnston, a former member of Unifor Local 88 who no longer works at the CAMI plant. “What if there is no public uptake or there’s a change in direction? Have we put enough thought into EVs as a society, or are we just forcing it along before it’s fully baked? If we can’t meet demand, will our markets just go elsewhere?”
CAMI plant worker and union officer Mark Gee also expressed concern about supplier readiness. “We need to consider supply-chain vulnerability when initiating any greener tech,” he said. “Will our suppliers be ready with the parts and raw materials?”
The growing EV industry has created demand for new skills in the local labour force. “We cannot just shift the local workforce from the production line to meet new technical requirements and processes in greener industries,” said Jeff Surridge. “For example, EV plants are heavily automated compared to old-school automotive plants. And 80 per cent of this new workforce will now require specific technical skills.”
“Employers can’t just steal the talent from other sectors — those skills don’t yet exist,” he added. “Sure, we might be able to find one or two specialists as needed but the problem is scalability across a whole workforce, especially with new and changing technologies.”
GM provided its own training to the workers at the CAMI plant. It initially sent a team to the U.S. to work with an engineering group. The team then came back to pass along the knowledge to plant workers through a mix of on-the-job and classroom training.
Some interviewees raised the need for more broad-based training programs. “Understand that many plant workers only have high school education and may need upgrading to prepare for [advanced] education programs, not just short training for other vulnerable jobs,” said Charlotte Johnston. “Training programs [need] to be for a more broad-based education, not just quick training for a specific job that is probably just as precarious,” she added.
Several interviewees called for more flexibility in program eligibility, funding support, delivery mode and choice of subject matter. Some adult learners are unable to devote themselves to full-time study due to inadequate prior education, family obligations or part-time work needed to make ends meet. According to Gee, some displaced GM workers decided not to participate in the training offered by GM because the funding support was not sufficient to support their families and meet their household financial obligations.
“Those who are being forcibly removed from their sector should have priority for retraining into good future-oriented jobs,” suggested Johnston. “Maybe those who are getting displaced by green technology could be specifically coded so they would have expedited access to learning programs.”
Surridge suggested that “developing more community- or employer-specific training programs could allow for much-needed flexibility. However, this type of place-based consultation and planning also downloads a significant responsibility to smaller communities with limited resources,” he said.
Conestoga College’s Ingersoll Skills Training Centre offers one of the few power line technician programs in southwestern Ontario. The two-year hybrid program provides instruction on construction, maintenance and repair of overhead and underground power-distribution systems.
Like training programs, the eligibility rules for Employment Insurance do not adequately accommodate part-time, short-term or periodic layoffs, or delayed startup employment as companies ramp up production of new products, Johnston said.
Several interviewees agreed that EI does not currently allow for sufficient time to go through more comprehensive training programs and does not take into consideration that two primary wage-earners in one family may be employed by the same employer.
EI eligibility should also consider all those who work in an affected community and are caught in a workforce transition by a major local employer, Johnston said. “We need to look at all the affected businesses. There are many downstream effects on jobs, like one supplier with almost 150 employees had to close when CAMI was shut down, and even Tim Horton’s was hurting,” she said.
There are several solar and wind projects in the Ingersoll area, including the 18-megawatt Gunn’s Hill windfarm, the 10-megawatt Ingersoll 1 solar project and the 10-megawatt Breen 2 solar project.
Wind energy came up in many interviews, with some viewing it as a resource and an economic opportunity that could be compatible with agricultural land use, while others called for a more cautious approach to encroachment on private lands. Some residents have strongly opposed wind energy developments.
“There are real opportunities for growth in wind energy,” said Helmut Schneider, of Prowind Renewables and the Oxford Community Energy Co-op, who is involved in promoting wind development. “Look at the EU uptake on wind energy,” said Schneider. He pointed out that there are roughly 10 times as many wind turbines in Germany as in Ontario even though Germany has one-third the landmass.
“We need to encourage municipalities to be interested in, or at least not resistant to, wind turbines; not to ban the turbines outright but to conduct proper research, due diligence, consultation and partnership-building to develop more nuanced guidelines,” Schneider said. “Landowners should have the final say, to choose whether to install a turbine on their land.”
In Ontario, the provincial government has given municipalities veto power over new energy generation projects. More than 150 municipalities, including parts of Oxford County, are unwilling to host wind turbines due to land use, noise, health impacts, loss of sight lines and other concerns.
The shutdown of the CAMI plant and the ongoing layoffs have demonstrated the importance of community resources and social service supports for workers going through displacement and transition and others in the community. Some interviewees reported that there were increases in depression, anxiety, stress, domestic abuse, addictions, financial hardship, illness and mental health problems. These were compounded when more than one breadwinner in the household was employed with the same company.
For an employer about to go through a workforce transition, community leaders suggested more proactive planning to anticipate mental health concerns in times of high stress and uncertainty.
One approach could be to create a strong planning and response group with representatives from the company, workers, governments, health-care providers, and other local agencies and service providers. Such a community wellness strategy should begin well in advance of the planned workforce disruption. Addressing how the supports can be accessed will be as important as what supports are being put in place.
In many ways, the transition of GM’s CAMI plant to a fully electric motor-vehicle assembly facility is a community success story. Government investments in GM’s Ingersoll plant and throughout southern Ontario hold the potential to kickstart a new direction for the local economy, the province and the country. GM workers and community leaders are proud of being on the vanguard of the EV transition.
However, Ingersoll’s experience also illustrates the challenges of managing a workforce and community transformation and the many questions there are to resolve along the way. Workers have lingering concerns about whether the demand for EVs will be strong enough to sustain production, whether the appropriate skills and training programs will be available to meet the needs of the new workforce, and whether EI eligibility rules are up to the task of supporting workers affected by periodic layoffs while plants close and retool.
Community leaders are concerned about providing adequate support programs and social services to help workers and residents weather the hard times. Employers are seeking government support in expanding EV supply chains and infrastructure, including transmission lines, charging stations, electricity production and critical minerals, and in building consumer demand for EVs.
These questions are top of mind for Ingersoll community leaders, employers and residents. To make the transition a success, they want governments to listen and respond to their concerns, and provide the following:
The Institute for Research on Public Policy (IRPP) has developed a methodology for measuring community susceptibility to workforce disruption as global efforts to address climate change expand. Using three indicators, the methodology scores and ranks census divisions across the country. Based on their ranking, each census division is assigned to one of six groups, ranging from “not susceptible” to “most susceptible.”
The three indicators include Facility Susceptibility (emissions from large facilities relative to the size of the community), Intensity Susceptibility (proportion of employment in emissions-intensive sectors), and Market Susceptibility (proportion of employment in globally traded sectors expected to undergo market transformations).
The analysis is available in an interactive map, developed in collaboration with the Community Data Program of the Canadian Community Economic Development Network, on the IRPP’s website (irpp.org/community-transformations). A detailed description of the methodology used is also available on the website.
To complement the mapping exercise, the IRPP selected 10 communities across the country to profile through a series of interviews with people who live and work in the community. Most of the communities selected are located within susceptible census divisions, but others were chosen because of anticipated developments or previous experiences. The profiles are meant to cover a diversity of regions of the country and types of economic activity. These snapshots provide additional insight into the challenges and opportunities the communities face and to reflect the perspectives of residents.
Ingersoll, Ontario, is one of the communities selected. It was chosen because the census division in which it is located — Oxford County — was more susceptible than other census divisions in Market Susceptibility. The score reflects the high proportion of employment in transportation equipment manufacturing, mainly motor vehicles and auto parts. Ingersoll is also the location of General Motors’ CAMI Assembly plant, one of the country’s first full-scale electric vehicle manufacturing plants.
The Energy Mix and the IRPP conducted interviews with community members in Ingersoll, the third-largest municipality in the Oxford census division. The IRPP also visited Ingersoll to tour the CAMI plant.
Below, we present a breakdown of the susceptibility analysis for Oxford County, which includes Ingersoll, Woodstock, Tillsonburg, Norwich and Zorra. Additional information not used in the analysis, such as population change, the unemployment rate and demographic characteristics of workers, is derived from the 2021 census.
If you have questions about the profile or the analysis, please contact us at communitytransformations@nullirpp.org.
This Community Profile was published as part of the IRPP’s Community Transformations Project. It was authored by The Energy Mix and the IRPP. The manuscript was copy-edited by Rosanna Tamburri with assistance from Abigail Jackson. Ricardo Chejfec was responsible for the data analysis. Proofreading was by Zofia Laubitz, editorial co-ordination was by Étienne Tremblay, production was by Chantal Létourneau, publication management was by Rosanna Tamburri and art direction was by Anne Tremblay. Photos are by Yaira Estrada-Wagner and courtesy of GM Canada.
The Community Transformations Project was funded in part by The McConnell Foundation and Vancity. Research independence is one of the IRPP’s core values, and the IRPP maintains editorial control over all publications.
A French translation of this text is available under the title Ingersoll : la ville ontarienne qui mène la transition vers les VE.
To cite this document:
Institute for Research on Public Policy. (2025). Ingersoll: Ontario auto town grapples with the EV transition. Montreal: Institute for Research on Public Policy.
We’re grateful to the following people for sharing their ideas, experience and time with us.